First, the status quo of the bearing “running circle” problem
The so-called bearing “running circle” is that the outer ring of the bearing and the bearing seat or the inner ring and the shaft have a relative movement. The planetary gear of the gearbox has a running ring that will cause irreparable damage to the gearbox.
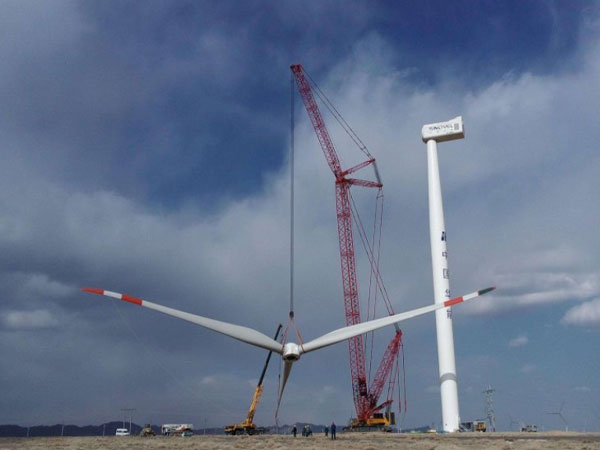
Since the beginning of 2015, the running wind turbines have gradually exposed the problem of gearbox bearings “running circles”. According to incomplete statistics, in recent years, more than 100,000 units installed in China have suffered from “bearing running circle” failures, accounting for more than 10%. Not only are the double-fed motor units with more bearing applications, but also the main drive system bearings. Similar failures occurred in fewer direct-drive units, and the total number exceeded 1,000. According to a team of power equipment research institutes who recently measured the results of a group of operating units, the vibration spectrum showed a fairly high percentage of the unit’s running problems (according to what they say is almost 100%). Some units of foreign manufacturers also have bearing running problems. From the overall situation of the found bearing “running circle”, the high-speed end of the gearbox has a higher proportion, and the proportion of the planetary gear bearing “running circle” is lower. However, in the products of several manufacturers, the proportion of “running circles” of planetary gear bearings is relatively high, and batch failures occur.
The loss caused by the bearing running circle will greatly increase the operation and maintenance cost of the wind turbine, and may also affect the insurance company’s premium rate in the future.
At present, most of the domestic manufacturers, developers, and insurance companies that have bearing running circles do not understand this situation. The faults are handled by the gearbox factory itself, and the customer’s transmission is not truthfully told. In this case, this high-risk, high-cost failure has become a huge potential risk in the wind power operation and insurance industry.
Most of the handling of the “running circle” failure of the high-speed end bearing of the gearbox is solved by inserting or using a polymer binder after the fault is discovered. These two methods have relatively mature experience in ground equipment, but for the high-speed end bearing of the wind turbine gearbox, whether it can guarantee long-term use after repair, there is no mature experience.
For the planetary gear bearing “running circle”, there is no mature technology that finds the “running circle” fault in advance in China, and the difference in the spectrum of the bearing “running circle” due to the difference between the unit form and the operating environment, so most planetary gears Bearing “running” failure is confirmed after the transmission is damaged.
For the main bearing running ring of the direct drive unit, if no obvious damage is found in the bearing, the method of adjusting the bearing clearance is adopted; if the bearing is damaged, the main bearing is replaced.
Second, the analysis of the problem of bearing “running circle”
It is fundamentally due to improper bearing selection, improper structural design and load design, improper process control during manufacturing, improper adjustment of bearing clearance, improper bearing lubrication, improper storage or transportation of equipment, etc., resulting in bearing roller and bearing raceway. Severe sliding semi-dry friction occurs, eventually leading to the bearing “running circle”.
1. Spindle bearing
(1) The main shaft bearings of MW-class wind turbines with double-row spherical roller bearings are subjected to axial and radial loads at the same time, and the probability of failure is high. This is because the double row spherical roller bearing has a large clearance, and the bearing on the upwind side bears a small load. Most of the radial load and the axial force are received by the downwind bearing, causing excessive roller slippage. Poor lubrication causes the material to change from pitting to sticking, the seat ring and the roller and the cage are deformed unevenly, which changes the coordination between the race and the bearing seat, and causes common faults such as “running circle” and jamming.
(2) When designing the new transmission system, the spindle bearing has rarely used the self-aligning bearing. It is recommended to use the tapered roller bearing. The radial and axial bearing capacity is strong. The roller can be evenly loaded by pre-tightening, and the roller is not easy. Produces sliding friction. However, due to the high installation and technical requirements of the assembly process, improper adjustment of the bearing clearance can still cause semi-dry rolling friction, and then run-loop failure.
(3) The bearing assembly adopts the hot charging method. Since there is not enough heating device, the local heating method is used, and the heating is uneven, resulting in bearing deformation.
(4) During the transportation process, the unit’s damping measures are improper, or a part of the bearing is bearing for a long time, causing local deformation of the raceway.
(5) There are two main lubrication methods for the main shaft bearings of wind turbines currently in operation: grease lubrication and pressure lubricant lubrication, in which the lubricating oil with a higher proportion of lubrication is generally 10-20 rpm, which is low. The rotational speed of the spindle bearing and the planet carrier support bearing is often difficult to form. If the thickness of the oil film is insufficient to separate the two metal surfaces, the lubrication does not achieve the predetermined effect, the bearing will wear out early, the material peeling damage will occur, and the semi-dry sliding friction will occur, which in turn will cause the bearing to run. The pressure lubrication method is very beneficial to improve the working condition of the bearing. In addition to forming the oil film to protect the rolling roller in time, it can also take away heat and abrasive grains to prolong the service life. It is recommended that the spindle bearings be lubricated with pressure oil if conditions permit.
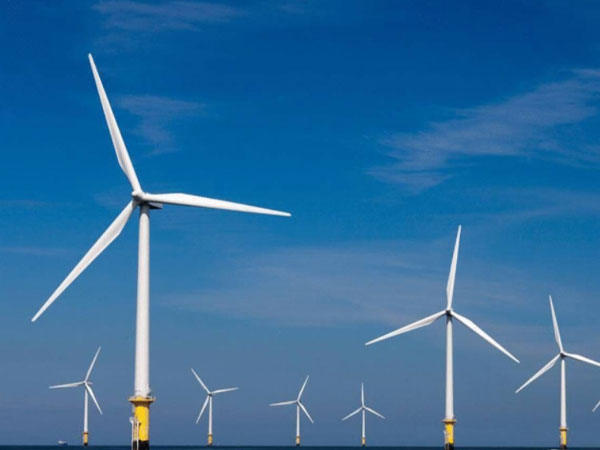
2. Transmission bearing
The ratio of the running ring of the high-speed shaft-side bearing in the gearbox is higher than that of the planetary gear bearing, and the reason for the difference is different.
3. High speed shaft side bearing
(1) The matching tolerance of the bearing and the bearing housing is unreasonable, resulting in insufficient interference. Since the external environment in which the wind turbines operate varies greatly, it is very likely that the standard tolerance zone will not be able to adapt to the operating conditions.
(2) The process control during assembly is not strict, which results in the matching of the limit deviation between the bearing and the bearing seat and the deviation under the limit. At the assembly site, it has actually been found that the assembler selects a bearing with a small amount of interference for fitting.
4. Planetary wheel bearing
(1) The maximum power of the wind turbine gearbox in actual use may reach more than 3 times of the nominal power. Especially in the case of growing blades, the moment of inertia of the wind turbine is greatly increased, and the impact load on the drive train during the start and stop of the unit is increased. It also greatly increased the domestic unit to increase the blade on the basis of the prototype, and did not redesign the gearbox accordingly, resulting in the case of the gearbox planetary shaft system and the intermediate shaft system with relatively poor rigidity. The load increases the occurrence of bearing stress concentration, which in turn causes the bearing to run.
(2) The planetary gear train structure design is weak. The national standard GB / T19073 wind turbine gearbox specifies that the thickness of the planetary gear hub should not be less than 3 times the modulus, in order to ensure that the gear race has sufficient rigidity to resist the deformation caused by the gear force. The deformation of the planetary gear is one of the important reasons for the bearing running circle. The gearbox failure of the planetary gear bearing in the domestic gearbox factory occurs precisely because the design does not meet the thickness requirements of the gear hub proposed by the standard.
For the planetary shaft system, the floating planetary gear shifting mechanism is adopted abroad to achieve the purpose of uniform loading. However, such structures are more complicated in gearbox assembly and adjustment.
Aiming at the situation that the planetary gear structure size is difficult to meet the rigidity requirement due to the space limitation of the wind turbine, the solution of integrating the planetary gear with the bearing outer ring and the integrated flexible pin scheme similar to Timken (see Figure 1) are proposed abroad. Several gearboxes have been trial-produced by the domestic Hangzhou Gear and the South High Gear with integrated structure and integrated flexible pin structure. Since the planetary gears are machined, heat treated and tested in the gearbox and bearing factories according to the machining process, the cost of the gearbox is greatly increased. Domestic wind power machine enterprises are difficult to accept under the current market price. Foreign machine companies have adopted gearboxes of this type in batches.
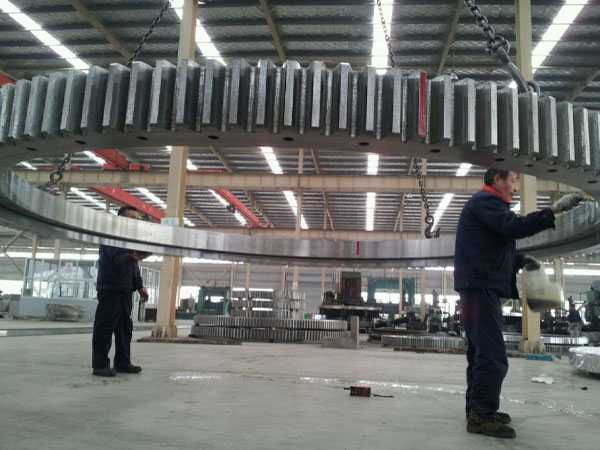
Suggestions based on current realities:
1. From the current situation reflected in all aspects, it is imperative for the wind turbines that have been put into operation to find the harbinger of the bearing running circle in time before the destructive accident. This can eliminate the accident in the bud. However, due to the different structure of the wind turbine, the operating environment is different, the bearing positions are different, and the vibration characteristics of various types of bearing running rings have not been mastered technically. What can be done at present is to collect the vibration monitoring records of wind turbines that have already had accidents, organize professional teams to analyze them, find out the regularity items as soon as possible, and then verify and promote them in the running wind farm. There are already a number of manufacturing companies, development and operation companies and research institutions expressed their willingness to participate and provide verification conditions.
2. The analysis in front of this report is based only on previous theories, experiences and available cases. The current large number of accidents have not yet been fully grasped. In order to conduct an accident analysis, each gearbox manufacturer should no longer use the pretext of keeping the so-called “trade secrets” as an excuse to refuse public accidents. The result of this can only cause deeper damage to China’s wind power industry. Only by thoroughly grasping the real situation of the accident in the industry and thoroughly analyzing the possible causes can we find the root cause of the defect and take effective measures to solve it. At the same time, provide basic data for mastering accident monitoring and early warning technology. It is recommended that all enterprises involved in similar accidents should truthfully provide accidents to the whole machine enterprises, development and operation enterprises and research institutions.
3. Bearings should be equipped with sufficient tooling to prevent invisible damage during assembly. The assembly with interference fit is preferably to uniformly heat the bearing by a closed heating device. The heating temperature should not be too high, and it is in a positive clearance state during the heating process, and does not squash the roller and deform. When conditions permit, it is recommended to assemble the bearing by means of a freezer shaft. The lubrication of the bearings should be highly valued. In addition to ensuring adequate lubrication, adequate measures must be taken to ensure the cleanliness of the fluid.
4. In the selection of bearings and their cooperation, the host and components and the bearing supply unit should work closely together, timely exchange and feedback, and reasonable selection of bearings and cooperation. The shaft and hole of the bearing of the device should be selected according to the tolerance of the diameter of the bearing ring, and the tolerance range should be properly tightened to ensure the interference of the fit.
5. Strengthen the training and training of professional and technical workers to ensure that the assembly and clearance adjustment of the bearings meet the technical requirements.
6. During the assembly process, the shafting should be centered repeatedly to mitigate the effects of additional loads.
7. Strengthen the processing of gearbox, the technical procedures of the assembly site, the process hygiene management, ensure the processing of the gearbox, and the assembly process is carried out under strict process conditions.
8. Prepare technical guidelines related to the transportation and storage of wind turbines and main shafts to prevent deformation of the lower end raceways and rollers of the main shaft bearings due to the large gravity of the main shaft during transportation and non-operational stages.
9. Enhance the rigidity of the wind turbine frame to prevent abnormal eccentric load of each bearing caused by deformation.
10. Strengthen the daily maintenance of wind turbines, strictly abide by the safe operating regulations, and have sufficient countermeasures for the impacts of different processes such as starting, braking, stopping, and deactivating the unit.
11. The wind turbine should be equipped with relevant detection devices to perform instantaneous monitoring of the vibration and temperature of the transmission system, analyze the measurement data, accurately find the cause, and issue an early warning to avoid downtime due to failure.
12. Strengthen the design research of wind turbines. Based on the reliability analysis, the system analyzes the impact of the abnormal transient load on the key parts of the transmission system for the severe working conditions of the unit, and compiles the load spectrum that is more in line with the actual working conditions. Fully guarantee the safety margin of the system and components. Improve the layout and structure of the drive system to reduce the effects of transient anomalous shock loads.
13. Reasonably select the structural form of the unit transmission system on the basis of accumulated experience, and adopt the mature and proven transmission form as much as possible. The new transmission form and structural arrangement should not be easily adopted without demonstration.
14. The original bearing life calculation theory has been difficult to meet the requirements of modern wind turbine gearbox bearing calculations. The relevant information manufacturer of the new bearing life calculation method proposed by the international famous bearing company is generally less public. At present, the calculation of bearing life is generally estimated based on the life calculation method proposed by each bearing manufacturer. Bearing life calculation methods are numerous, the influencing factors are complex, the load data is scarce, and the complex load processing methods are imperfect. The processing of transient loads, braking loads, ultimate loads, etc., which are often encountered during the use of the unit, is estimated empirically. In addition, the linear cumulative damage theory used in the process of variable load processing does not truly reflect the actual damage, which will lead to an increase in the gap between design calculation and practical application. To this end, it is recommended to strengthen the research on the theory of domestic bearing life in combination with the actual needs of wind turbines.
15. It is recommended to strengthen the research on bearing design, materials, technology and inspection technology in the special field of wind power high load capacity, high reliability and long life as soon as possible. The bearing industry and wind turbine manufacturing enterprises, wind power transmission equipment manufacturing enterprises jointly carry out research work, accumulate experience for the design and manufacture of wind power bearings, and strive to make breakthroughs as soon as possible.