Crane is a common engineering machinery equipment. It is mainly used in the construction of bridges, roads, and port projects. Due to the working environment and overloading, there is often no turning action during work, which not only affects the overall performance of the equipment, It also delays work efficiency. Today, we mainly introduce the causes and troubleshooting methods of common crane rotation failures.
The crane does not rotate, mainly dues to the mechanical transmission of the slewing mechanism or its electronic control system fail. Today, we mainly discuss the non-rotational failures of tower cranes (Towers) and gantry cranes, analyze the causes of the failures, and propose ways to eliminate them.
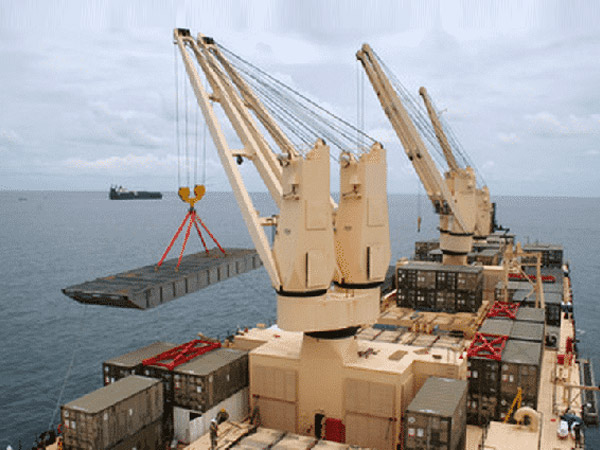
First, mechanical failure
The slewing bearing of the crane acts as a connection between the upper and the chassis in the slewing mechanism while supporting the entire rotating portion of the crane. The main cause of mechanical failure: slewing bearing wear. When the crane works in an environment with strong corrosiveness and dust, or after large rainwater has passed, the steel ball in the slewing bearing is damaged and the raceway is worn. Both will affect the work of the slewing mechanism. In severe cases, the slewing mechanism will experience heavy rotation and noise. Violation of the operation, such as lifting the weight, when using the basic arm of the crane to pull and tilt the heavy objects in the distance to achieve the purpose, often erroneously use the slewing mechanism to diagonally pull, this is a violation of the safe operating procedures. At the same time, the slewing mechanism and the basic arm are also damaged.
Remedy: Repair or replace the slewing ring bearing. Wipe in time, add a proper amount of lubricant to the inside of the slide, and apply some anti-rust oil to the outside. The grease nipple should be unblocked frequently to prevent clogging, and the tightness of the bolts everywhere should be checked frequently to prevent the gap between the upper and lower landslides from being too large due to the looseness of the bolts, resulting in wear of the steel balls and raceways.
Second, the rotary hydraulic system is low
When the pressure of the rotary hydraulic system is low, the sound and speed of the rotary process are normal under the condition of the no-load or light load of the crane; when it is heavy, there will be difficulty in turning or even no turning. The reason for this phenomenon is that the spring of the overload buffer valve of the rotary hydraulic system is softened. The pressure of the rotary hydraulic system is realized by adjusting the screw of the overload buffer valve. This adjustment screw also has the function of sealing the oil passage. In order to ensure the sealing of the oil passage, the screw must be tightened, but the spring cannot be adjusted at will. The pressure is gone. Remedy: When the spring pressure is not enough, only use the spring end to add a washer to solve or replace the new spring.
Third, the rotary electronic control system has failed
First, the rotary motor burns or the carbon brush breaks to produce a short circuit, and the carbon brush wears to cause an open circuit with the slip ring; the second is that the brake electromagnetic coil is burnt, causing the brake friction plate to lock and can not release the brake; the third is the electronic component The damage is broken or the fuse is blown; the fourth is the damage of the contactor that controls the rotation; the fifth is the damage of the relay that controls the rotation; the sixth is the poor contact of the electrical part of the main controller (the main switch).
Remedy: If the rotary motor burns, it is often caused by excessive load, phase loss of the three-phase power line or short circuit. If the slewing load is too large and the three-phase power line of the slewing motor is out of phase, the motor will be burnt. At this time, stop the operation immediately. Carbon brush breaks are prone to short circuits and high-quality carbon brushes should be used. The carbon brush should be maintained in time to replace the carbon brush with excessive wear. If the brake solenoid is burnt, check the solenoid. When checking, turn on the power of the electromagnetic coil to be inspected, and use a screwdriver to check whether the electromagnetic coil generates suction force to the screwdriver. If there is suction, it means that the electromagnetic coil is not broken, otherwise, the electromagnetic coil is broken, and the new electromagnetic coil should be replaced. Also, check the brake lining wear and replace if necessary. If the electronic component is damaged or its fuse is blown, replace the fuse in the electronic component or electronic component. If the contractor and relay that control the rotation are damaged, replace the new one. If the main controller of the swing is in poor contact, adjust or replace the contact or master controller assembly.
If there is a crane rotation failure during work, it should be stopped immediately to prevent the equipment from working, which not only affects the performance of the whole machine but also greatly reduces the life. Luoyang Hengguan Bearing Technology Co., Ltd. is a comprehensive enterprise integrating slewing bearing design, research, and development, production, sales, and service. If you have any other questions, please contact us.