Slewing bearing , also known as a rotary bearing or rotating support, is a mechanical element specifically designed to support and allow rotating motion. It is usually composed of the internal and external ring, roller, roller or roller, and sealing. It can be used for various industrial applications. From small machinery to large engineering equipment, it is an important mechanical element in various fields. It is rotating equipment and The mechanical system plays a key role. This article explains some explanations for the role of re -supporting support.
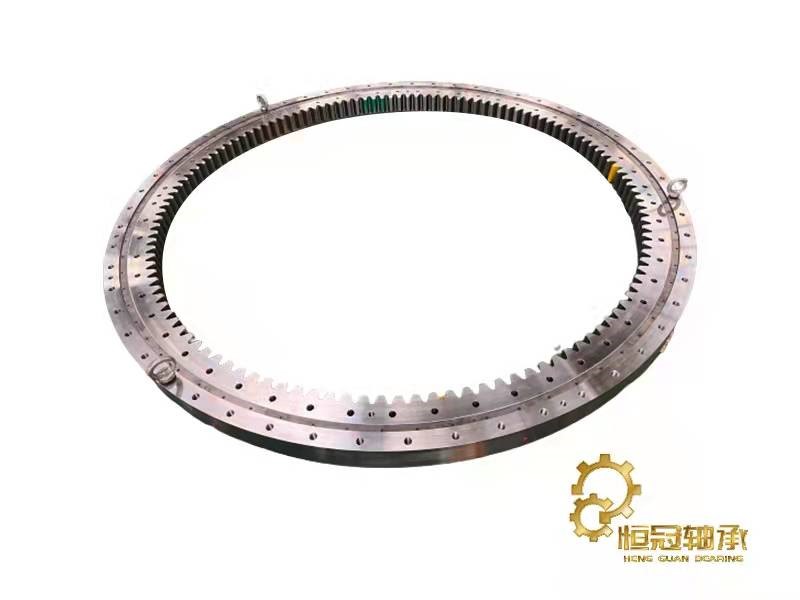
The role of the slewing bearing
1. Support rotation exercise
The main role of rotating support is to support rotation movements. It allows equipment or mechanical parts to rotate around the axis in a smooth way to achieve the operation of the equipment. This is very critical for applications that require continuous rotation or periodic rotation, such as various types of rotating platforms, robotic arms, wind turbines, etc.
2. Undertaking pile
The slewing bearing can withstand various loads from the rotation device, including radial load, axial load and torque. Through the appropriate design and material selection, the rotation support can withstand highly complex mechanical requirements and maintain the stability of the system.
3. Implement accurate positioning
In some applications that need to be accurately positioned and directed, rotation support is very important. It can ensure that the device can accurately stop at the required position when rotating, thereby meeting the accuracy requirements of production or operation. This is particularly important in the fields of machine tools, automation devices and observation equipment.
Rotate support 4. Reduce friction and energy loss
Slewing bearing is usually very precise. Rolling elements such as rolling or rolling are used, which helps reduce friction and energy loss. This makes the rotation movement more efficient, reduces energy consumption, and extend the service life of the equipment.
5. Reduce maintenance cost
Good design and high -quality rotation branches usually require less maintenance work. This reduces the stop time and maintenance cost of the device and helps improve production efficiency.
As a mechanical element, the rotary support has many effects of rotation support. They support rotation movement, tolerance, accurate positioning, reducing friction and energy loss, and also help to reduce maintenance costs. The design and application of rotating support has become an indispensable part of the modern engineering field, and promotes the development of various industrial and technological applications. Whether in the fields of construction, energy, manufacturing, and medical fields, the re -supporting support plays a key role in improving equipment performance, improving production efficiency, and ensuring safety.