Rotary kiln large gear ring processing manufacturers can produce various large gear rings according to drawings, and can ensure the product quality of large gear rings. So how should the large gear ring be adjusted during use?
1. The construction process of the rotary kiln large gear ring is as follows: divide the circle between the large gear ring and the cylinder into four equal parts, make a tool bracket for disassembly and adjustment, and fix the large gear.
Remove the bolts and locating pins at the connection of the two rings, and use a carbon arc air gouging to remove the spring sheet connecting the large gear ring to reduce the burn to the cylinder when removing the weld. After all the welds of the spring sheet are removed, use a crane to lift the two gear rings to the hard and flat ground on site, and then remove the connecting bolts between the spring sheet and the large gear ring. The connecting hole between the large gear ring and the spring sheet is re-drilled, and the bolt size is determined by the matching hole size. After the pinion and shaft are lifted and removed by the crane.
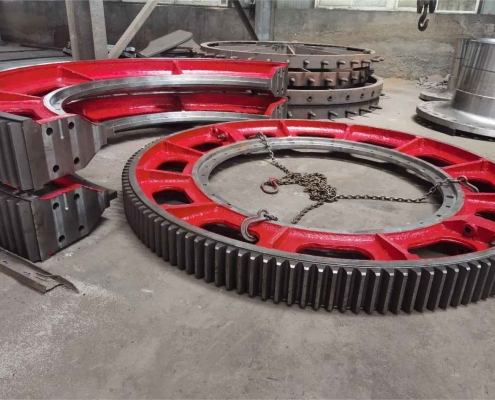
2. Correction of the rotary kiln large gear ring and spring plate. Lift the gear ring onto the prepared fixture bracket, and tighten the connecting bolts and positioning pins at the connection of the two gear rings of the large gear ring. Ensure that the joints of the two half teeth fit tightly, and use a 0.04mm feeler gauge to check around the mouth, with an insertion depth of no more than 100mm. Make two micrometer fixtures to detect the radial and end face swing of the large gear ring, divide 12 measuring points equally around the large gear ring, and use a rotary kiln to divide 12 measuring points equally around the large gear ring, record the test values, and adjust the radial and end face swing values of the large gear ring through the bracket and adjustment fixture installed on the large gear ring. Now, the large gear ring has been running for several years. When adjusting, the radial and end face swing values of the adjusted large gear ring should be controlled within 2.0mm and 2.5mm as much as possible under the premise of satisfying the normal operation of the large gear ring. Only after the radial and end face swing values of the large gear ring are adjusted, can the connecting spring sheet be installed. The spring sheet and the barrel should be polished flat and tightly connected. The spot welding and welding of the spring sheet and the barrel should be carried out symmetrically to reduce deformation after welding.
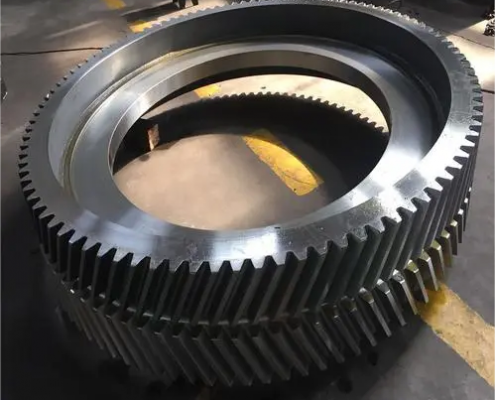
3. Correction of pinion, reducer, main motor and auxiliary motor. The clearance between the top of the pinion and the large gear should be controlled at 0.25M+(2-3)mm, the tooth surface contact, tooth height and tooth length should not be less than 40% and 50%, and the coaxiality of the pinion shaft, reducer, main motor and auxiliary motor transmission shaft should be controlled at no more than 0.2mm.